Flue Gas Treatment and Separation
Coal fired power plants are considered the largest emitters for CO2. Membranes can dramatically help reduce the carbon footprint of these power plants by removing CO2 from the plant flue gas. GENERON’s® Flue Gas Treatment Systems can be used to remove the CO2.
GENERON® supplies customized flue gas treatment membrane systems which also include the feed compression. GENERON® fabricates its own membrane filters and works directly with the client to provide the most efficient and cost effective solution.
An alternative for treating the flue gas is an amine system which is complex and requires high capital, operating and installation costs, as well as chemicals that needs continual replacement and disposal.
The GENERON® Advantage
- Extensive Experience – custom designed skids
- State-of-the-art Membrane – high recoveries
- Simple Solution – no moving parts, minimal maintenance
- Remote Operation – Minimal attention required, fully automated systems
- Minimal Losses – low HC losses
- No Chemicals – environmentally friendly
- Small Footprint – easily meet footprint requirements
RELATED GENERON PRODUCTS:
- PSA systems
- Instrument air packages
- Air and gas compression packages
- Blowers
- On-site oilfield services – operating personnel and rental equipment
- Custom Integrated Skid Packages
In a typical GENERON® flue gas conditioning treatment membrane system the feed gas is first filtered to remove any particles and liquid condensate. The gas is then enters the GENERON® membrane filters.
The CO2 as well as any moisture permeate preferably through the membrane. The non-permeated gas, mainly N2, remains at pressure and can be vented or used for energy recovery.
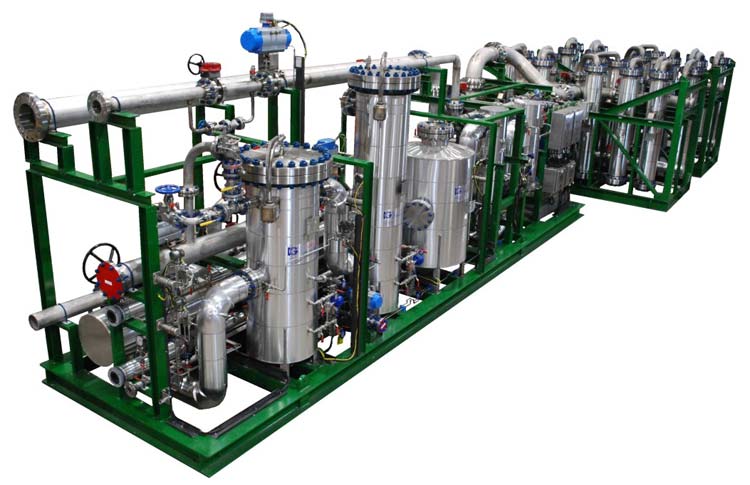
SYSTEM PERFORMANCE
- Feed gas pressures down to -100” H2O
- 5 – 20 vol% CO2 in feed
- < 2% CO2 content in product
- > 90% recovery of hydrocarbon gas
- > 90% removal of CO2
- Flow rates to 500 MMSCFD
FEATURING
- No moving parts, and designed for remote unmanned operation
- Efficient packaging minimizes space and weight – ideal for offshore applications
- Customized process design to maximize total hydrocarbon recovery
- System flexibility – Can operate at wide range of flow rates and CO2 Content
- Quick deployment & Installation – skidded system can be installed in hours
- C3 + Recovered = Revenue